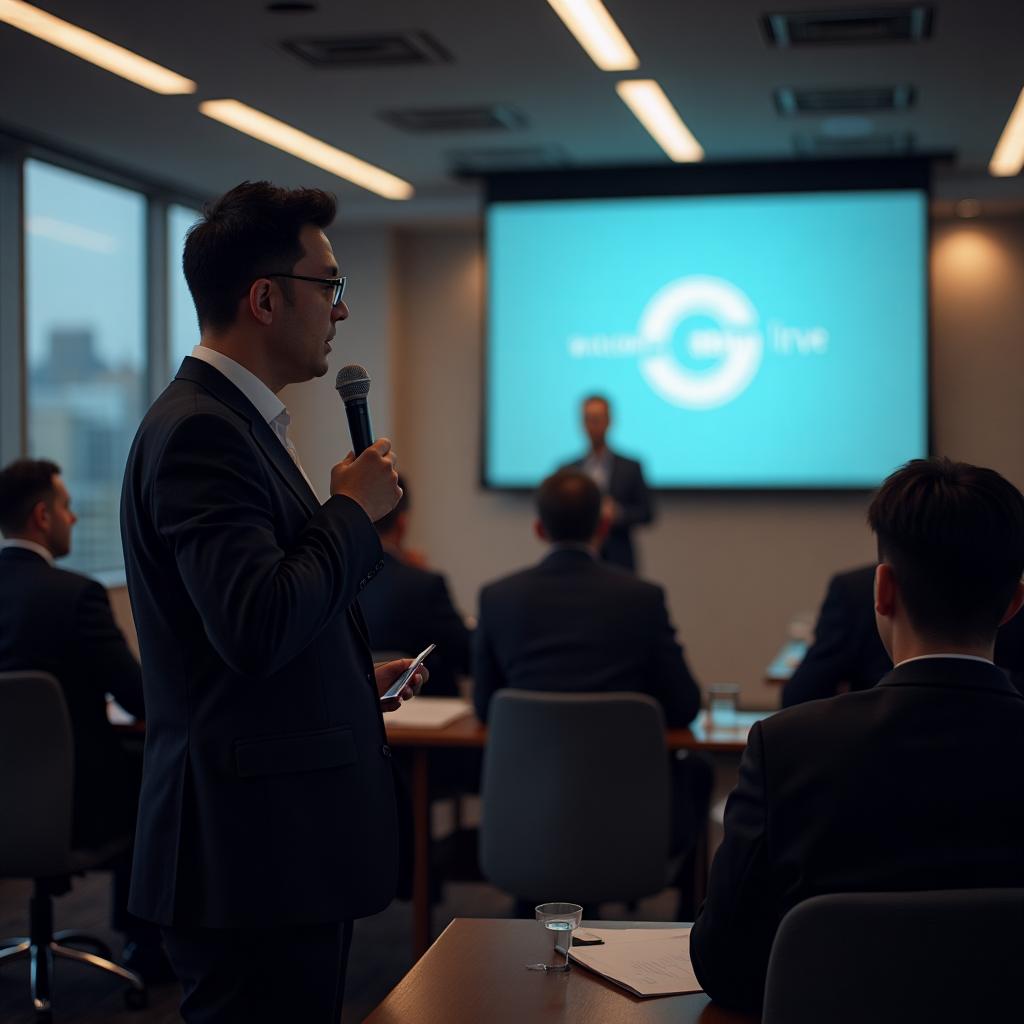
- Key Takeaways
- Understanding Continuous Improvement Processes
- Key Methodologies for Continuous Improvement
- Benefits of Implementing Continuous Improvement
- Challenges in Adopting Continuous Improvement
- Steps in the Continuous Improvement Process
- Creating a Culture of Continuous Improvement
- Digital Tools and Data Analytics in Improvement Efforts
- Adapting Continuous Improvement Strategies
- Case Studies and Real-World Examples
- Conclusion
- Frequently Asked Questions
- What are continuous improvement processes?
- Why is continuous improvement important?
- What methodologies are used in continuous improvement?
- What are the main benefits of continuous improvement?
- What challenges might organizations face in adopting continuous improvement?
- How can a culture of continuous improvement be created?
- How can digital tools enhance continuous improvement efforts?
Key Takeaways
- Continuous improvement processes lead to better organizational performance overall while creating an environment and culture of innovation. Accept continuous improvement as a process to improve products, services, and processes over time to ensure long-term success.
- Whether in healthcare or manufacturing, various industries gain substantially from continuous improvement processes by realizing operational excellence and competitive advantages. Make your continuous improvement processes focus on overcoming key industry challenges and meeting customer needs.
- Key principles like a focus on the customer, an inclusive approach engaging all employees, and a reliance on data to inform decisions are foundational to successful continuous improvement. Align your continuous improvement efforts with strategic organizational goals. These are the things that will make the most difference.
- Utilize proven frameworks, PDCA, Six Sigma, etc., to inform your continuous improvement processes. Use continuous improvement processes aimed at cutting out waste and improving quality to create efficiencies and maximize value.
- Continuously evaluate your existing processes, dig deep to discover what’s driving the problem, and create your fix based on fact. Include cross-functional teams in the solution development process to build buy-in and collaboration into the solutions.
- To continue making progress through continuous improvement, focus on building a strong organizational culture fostered by devoted leadership. Foster a culture of employee feedback, and keep the momentum going with regular reviews and updates to your improvement strategies.
In today’s age, continuous improvement processes should be second nature for any business looking to improve operations and stimulate reinvestment. By shifting your attention to continuous improvement processes, you can eliminate waste and maximize efficiency, contributing to achieving more meaningful results.
By adopting these continuous improvement processes, you can determine where improvements can be made, be it in the manufacturing process, service delivery, or management. As long as you’re focused on continuously evaluating and adjusting your strategy, you can help cultivate a culture of innovation in your agency.
Ideally, we should not only respond to problems as they emerge. Our goal is to establish an ongoing, sustainable framework that institutionalizes regular review and revision practice.
In upcoming posts, I’ll share other practical strategies to make your organization’s continuous improvement processes more effective and meaningful. You’ll learn frameworks for implementing these strategies that lead to continuous improvement processes.
Understanding Continuous Improvement Processes
Continuous improvement processes are the rigorous application of processes that improve individual and organizational performance. This process is pivotal to maintaining a managerial focus on quality and guaranteeing that products and services consistently meet or exceed customer expectations.
It encourages continuous improvement, smart innovation, and adaptability in all sectors—manufacturing, services, you name it.
What is Continuous Improvement?
Continuous improvement is a long-term, company-wide endeavor to improve the quality of products, services, and processes. It rewards organizations that choose to pursue modest, achievable improvements over the long term that result in truly transformational improvements.
For example, implementing KAIZEN™ principles promotes an environment where everyone contributes to improvements, enhancing performance and customer satisfaction. Beyond individual projects, this method encourages a culture of innovation, empowering organizations to be more agile and responsive to shifts in the market landscape.
Importance Across Different Industries
The power of continuous improvement is being seen in many different fields and industries. As one example, Lean methodologies in manufacturing place a heavy emphasis on waste elimination and efficiency gains.
Meanwhile, in medicine, continuous improvement processes improve patient safety and quality of care and are centered on operational excellence. Organizations that embrace these people-centric practices stand to gain a clear competitive advantage, better serving their customers’ rapidly evolving expectations.
Foundational Principles of Effective Processes
Key principles underpin effective continuous improvement, including employee involvement and systematic evaluation. Involving employees empowers employees through methodologies such as Lean Management and ensures that your entire team is tuned in to what drives efficiency and quality.
Aligning improvement efforts with organizational goals ensures the greatest impact. Consistent retrospectives are beautiful because they truly foster a culture of ongoing improvement.
Key Methodologies for Continuous Improvement
Continuous improvement processes are a must in today’s hyper-competitive climate. They serve as a continuous process improvement tool to help organizations identify and eliminate inefficiencies, thereby delivering even more value through structured approaches.
Overview of Continuous Improvement Frameworks
Popular methodologies such as PDCA (Plan-Do-Check-Adjust) and DMAIC (Define-Measure-Analyze-Improve-Control) inform these iterative, experimental processes. PDCA stresses an iterative cycle to test and refine in small bites.
DMAIC emphasizes using data to make decisions to reduce defects and increase quality.
Key Features:
- PDCA: Cyclical method Embrace a culture of continuous iteration Flexibility and applicability to many industries
- Equity-focused Data-driven Priority on quality assurance Structured problem-solving
Lean Methodology Explained
The lean methodology, developed by Toyota, truly focuses on eliminating waste and increasing value. It requires the participation of all employees in a firm, soliciting feedback and ideas for running operations more efficiently.
Core tenets include continuous flow, ensuring work proceeds in an even rhythm, respecting people, and creating a culture of problem-solving and teamwork.
Six Sigma Approach
Six Sigma, a highly data-driven methodology, was created in the manufacturing sector to achieve only 3.4 defects per million units. This continuous improvement model relies on statistical analysis as a process improvement tool, enabling teams to analyze root causes and develop solutions effectively.
Total Quality Management Insights
Total Quality Management (TQM) strives for long-term success by focusing on customer satisfaction. Its key elements, such as top leadership commitment and employee participation, support the continuous improvement model, making it the overarching goal of everybody within the teams.
Agile Methodology Integration
Agile methodologies are valuable for increasing flexibility and responsiveness within internal improvement initiatives. They emphasize collaboration, quick wins, and agile development.
This approach encourages adaptability to change, ensuring continuous enhancement aligns with evolving business needs.
Benefits of Implementing Continuous Improvement
Establishing a continuous improvement program has innumerable benefits for organizations focused on expansion and improved efficiencies. The main benefit is catching mistakes before they detrimentally affect customers. This proactive approach not only enhances operational performance but also lays the groundwork for long-term sustainability through ongoing efforts in process improvement.
Increased Efficiency and Productivity
With continuous improvement, you can achieve a more efficient operation – helping you do more with less and work smarter, not harder. With a targeted approach to key processes, entities have realized massive increases in efficiency.
Even improving cycle time by only 15% increases productivity by 28%. This demonstrates how small changes can lead to significant gains in overall performance.
Enhanced Employee Engagement
When employees are engaged in improvement initiatives, it fosters a culture of empowerment. Engaged employees are generally more positive and satisfied with their work, which has a clear ripple effect on performance.
For instance, teams that engage in routine brainstorming sessions frequently come up with more creative solutions to challenges. This engagement benefits the employees and enhances the organization’s overall problem-solving capabilities.
Waste Reduction Strategies
Focusing on removing waste is a key aspect of continuous improvement. Value stream mapping and frequent audits can be helpful strategies.
Common types of waste you might target include:
- Overproduction
- Waiting time
- Excess inventory
- Defects
Organizations can streamline their processes and improve overall efficiency by identifying and addressing these areas.
Cost Savings Opportunities
By implementing continuous improvement, organizations have already realized millions in cost savings. Better flow means less wasted time and energy, leading to major savings on operational costs.
For example, Lean strategic frameworks and action plans enable organizations to get as close to perfection as possible by eliminating defects and reducing waste. This focus on efficiency not only saves money but also enhances the organization’s competitive edge.
Improved Customer Satisfaction
The ongoing discipline of continuous improvement improves the quality of the products and services we deliver to create happier, more satisfied customers. When you start regularly seeking customer feedback, you can begin to get smart about which areas you should focus your improvement efforts.
This customer-centric approach ensures that organizations remain responsive to their clients’ needs, ultimately leading to better retention and loyalty.
Challenges in Adopting Continuous Improvement
Implementing continuous improvement processes can be challenging for many organizations due to resistance to change, insufficient staff buy-in, and limited resources. Overcoming these obstacles is essential for the successful adoption of a continuous improvement program and for maximizing the benefits of continuous improvement initiatives.
Common Pitfalls in Implementation
Common traps are lack of preparation, clear purpose or goals, and not engaging everyone from top staff to front-line employees. Staff could be left more confused and defeated without being honest about or addressing these issues.
To prevent these issues, set well-defined goals and involve team members early in the process. Engaging employees helps create ownership and ensures alignment with the organization’s vision.
Overcoming Resistance to Change
Whether right or wrong, managing employees’ resistance to change is essential. Employees can feel threatened by implementing new processes or fear learning something new.
Open lines of communication and adequate training can go a long way toward relieving those fears. Keeping people informed and delivering intentional workshops on the topic can create an environment more conducive to acceptance.
This collaborative approach contributes to a culture where everyone on your team feels empowered to engage in continuous improvement efforts.
Measuring Success and ROI
How we measure the success of these continuous improvement initiatives should be a top priority. Employ strategies, including surveys, audits, and performance evaluations, to measure and monitor outcomes.
KPIs KPI performance indicators, including reduced cycle times, cost savings, and employee satisfaction, must be tracked consistently. A bullet list of KPIs may include:
- Percentage improvement in process efficiency
- Reduction in waste or defects
- Employee engagement scores
- Customer satisfaction ratings
Steps in the Continuous Improvement Process
The continuous improvement process is a collaborative, data-driven approach that enables organizations to do their best work better and more efficiently. By adopting a more focused and flexible approach, you can pinpoint areas that need work and implement positive changes.
This method allows each step to be measured, providing a constant opportunity for refinement and improvement.
Assessing the Current Situation
Begin by evaluating your existing processes. Collect a comprehensive baseline of performance metrics, employee feedback, and customer satisfaction. Tools such as a process map are useful for illustrating the workflow and identifying bottlenecks or inefficiencies.
SWOT analysis, an acronym for Strengths, Weaknesses, Opportunities, and Threats, is a potent creativity tool. More importantly, it provides a window into the internal and external factors affecting that performance.
Identifying Root Causes of Issues
Equally important is getting to the root causes of those issues. Root cause analysis takes you underneath the surface of symptoms to find the trustworthy source of issues. The 5 Whys technique of root cause analysis prompts you to ask “why” several times to identify the root cause.
As with the Fishbone Diagram, visualizing where your potential causes lie makes it easier to analyze complex problems.
Developing and Implementing Solutions
Once root causes are identified, work to develop tailored solutions. Get cross-functional teams involved with this process to include many important and varied perspectives.
In big-picture STEAM learning, brainstorming sessions can quickly generate innovative ideas, and prototyping lets everyone test solutions before moving into larger projects. This intentional and collaborative approach ensures greater buy-in and measurably increases effectiveness.
Evaluating Outcomes and Standardizing Processes
Evaluate the outcomes of your implemented solutions. Gather evidence to show progress compared to your starting points. If successful, standardize these practices to ensure consistency across your organization.
This is where documentation comes in. Documentation helps keep those best practices on hand and is easy to find for anyone who needs them.
Creating a Culture of Continuous Improvement
Creating a culture of continuous improvement is essential for today’s organizations looking to be more productive and grow their bottom line. It’s about fostering a culture from the top down, bottom up, and everywhere in between, where every employee is equipped and empowered to recognize and address issues.
This culture improves morale and increases innovation. It allows the company to respond more effectively to the changing tides of the market and industry.
Leadership’s Role in Driving Change
Leadership is the essential ingredient to becoming a champion of continuous improvement. Leaders must do more than passively support initiatives; they must create a culture encouraging employees to share their ideas without fear.
When leaders model the behaviors they want to see, such as open communication, accountability, and a commitment to improvement, they inspire that same commitment in their teams. For example, when leaders get involved in improvement workshops, it shows everyone else on the team that improvement workshops are worth doing.
Importance of Employee Feedback
Soliciting employee feedback is a key component of creating a culture of continuous improvement. Employees frequently possess valuable, firsthand insight about processes, obstacles, and the best paths forward.
To solicit helpful team feedback, consider introducing anonymous surveys or weekly all-team huddles focused on sharing thoughts on how to improve. This not only makes employees feel valued but also creates a culture of ownership in the improvement process.
Best Practices for Sustaining Momentum
To build and sustain momentum in launching new continuous improvement initiatives, it’s essential to regularly revisit where things stand and what approach to take next. Creating a culture of accountability and continuous improvement with an ongoing process for measuring outcomes maintains alignment with desired goals.
Celebrating these small wins helps create a culture of continuous improvement, keeping the team committed and motivated. Frequent updates help ensure that all parties involved stay on the same page and abreast of changing strategies.
Digital Tools and Data Analytics in Improvement Efforts
The heart of digital tools and data analytics is advancing the discipline’s continuous improvement processes. They empower users with real-time, actionable insights that help them save time, improve workflows, and make better decisions.
Technology provides unprecedented visibility into processes and performance, which allows companies to spot inefficiencies and implement data-informed shifts that lead to improvements.
Enhancing Processes with Technology
Digital tools and data analytics power improvement efforts. For example, process automation tools like Zapier and project management software like Trello and Asana have been game changers.
These tools can take over the repetitive, low-value work, allowing employees to focus on higher-value, more strategic work. We’ve seen that when technology is an integral part of improvement initiatives, efficiency gains are achieved, errors are eliminated, and turnaround times are compressed.
For example, a factory that implements robotics and other automated processes may be able to reduce manufacturing time by 30%, dramatically increasing its capacity.
Real-Time Data Utilization
Real-time data analytics supports continuous improvement efforts by facilitating decision-making at the speed of need. Tools such as Google Analytics and Tableau provide timely feedback that brings instant visibility into agency operations.
They enable teams to diagnose problems quickly and identify areas for improvement. Data-driven insights are crucial for optimizing processes.
They allow businesses to respond promptly to changes in customer demand or operational challenges. For instance, a successful retail company can track sales data down to the second, literally.
This enables them to better calibrate inventory levels to reflect current trends, minimizing spoilage and maximizing customer satisfaction.
Adapting Continuous Improvement Strategies
Organizations need to adapt external strategies to their specific environments and cultures to embed continuous improvement truly. Every business works in different ecosystems, shaped by industry practices, operational capacity, and company culture among their workforce.
Customization is key to ensuring that improvement efforts align with an organization’s unique challenges and priorities.
Tailoring Approaches for Various Industries
Despite their new home in education, continuous improvement strategies differ significantly between industries. In health care, the most touted “continuous improvement” methodology — Lean — helps organizations improve and expedite patient flow and reduce wait times, improving the quality of care.
In manufacturing, Six Sigma principles help reduce product defects and improve the efficiency of the production process. For service sectors like hospitality, the priority may be developing employees who can better shape customer interactions, providing uniformity and customer satisfaction.
Rather, every industry needs to adapt techniques to meet its specific operational realities deliberately.
Customizing for Different Business Sizes
The size of an organization is another factor that significantly impacts how continuous improvement is utilized. Startups may benefit from agile methodologies that allow rapid iterations and adjustments, while large enterprises might implement more structured approaches like Total Quality Management to maintain consistency across multiple departments.
Allowing flexibility in the implementation process is essential. As organizations expand, diversify, or otherwise transform, their improvement strategies need to adapt to remain effective and relevant.
Case Studies and Real-World Examples
Navigating continuous improvement processes can only be learned by doing them in the real world. Case studies can show how communities, academia, and the private sector have widely adopted these practices and what they’ve learned from failed efforts.
This exploration encourages a more well-rounded view of continuous improvement, helping organizations get closer to truly practical approaches.
Successful Implementations in Various Sectors
Perhaps the most famous example is the automotive sector, where Toyota’s Kaizen philosophy transformed car production. Toyota dramatically cut waste and increased productivity by enabling all employees to spot inefficiencies and recommend better processes.
This resulted in a 50% improvement in production efficiency, demonstrating the tangible results that continuous improvement can bring.
In healthcare, Virginia Mason Medical Center used the Toyota Production System to deliver safer, more effective, and more efficient patient care. By reducing tired steps in their procedures, they cut patient wait times by more than 40%.
This success reminds us that the continuous improvement process can lead to better service for our riders and more efficient operations.
Lessons Learned from Failures
There are examples of organizations that fail in their continuous improvement initiatives. A high-profile case in point is a large retail chain that tried to roll out a cookie-cutter process without earning team member buy-in.
This lack of engagement led to overwhelming opposition and the initiative’s eventual failure. All of these common mistakes result from failing to include staff in the steps involved in creating alignment and understanding, resulting in a lack of alignment and staff frustration.
Conclusion
So get on board with continuous improvement processes to supercharge your business. You achieve greater efficiency, improved quality, and a culture that is more conducive to innovation. Every stage—from learning about new methodologies to utilizing digital resources—gets you one step closer to doing what you set out to do. Real-world case studies demonstrate the measurable outcomes provided by this paradigm shift. It’s all part of the making and taking, and it’s the making that’s so gratifying.
You need to begin somewhere, get your staff on board, and recognize your success early and often. 6 Continue to build and iterate on your strategies with input from the community and data. This commitment to continuous improvement processes sets you up for success over the long haul. So, leap into continuous improvement today, and let your business prosper.
Frequently Asked Questions
What are continuous improvement processes?
Continuous improvement processes are structured practices that utilize continuous process improvement tools to enhance an organization’s products, services, or internal operations. They focus on incremental improvements that foster efficiency, quality, and productivity.
Why is continuous improvement important?
Creating a continuous improvement program breeds powerful innovation and change. This ongoing effort empowers organizations to eliminate waste, enhance customer satisfaction, and increase competitiveness through structured approaches in a dynamic marketplace.
What methodologies are used in continuous improvement?
Some common methodologies, such as Lean and Six Sigma, serve as continuous process improvement tools that offer powerful strategies for overcoming inefficiency and finding and applying what works best.
What are the main benefits of continuous improvement?
Some benefits, such as operational efficiencies and improved quality, are key aspects of a continuous improvement program that fosters employee engagement and customer satisfaction.
What challenges might organizations face in adopting continuous improvement?
These challenges, such as resistance to change and lack of leadership support, highlight the need for a structured approach to continuous process improvement. Overcoming these obstacles is essential for successful implementation.
How can a culture of continuous improvement be created?
To create a culture of continuous improvement, promote collaboration, invest in learning, celebrate creative solutions, and include employees in strategic planning as part of a continuous improvement program. This feeds a sense of ownership and long-term commitment.
How can digital tools enhance continuous improvement efforts?
Digital tools and data analytics serve as essential continuous process improvement tools, enhancing data collection and analysis efficiency. By collecting these measures, organizations can track progress and identify necessary changes, ensuring their ongoing effort in the improvement journey.